POWER Paver Blocks
Paver Blocks
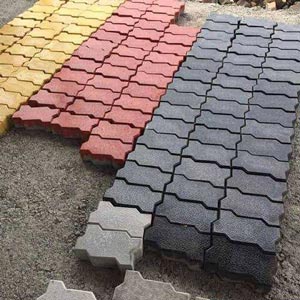
We manufacture Power Paver blocks which is one of the most flexible surface treatment for exterior & interior pavement applications. They are aesthetically pleasing, comfortable to walk, extremely durable, having latest pattern, available in different colours, design and thickness to give it an elegant look. We manufacture Power Paver blocks on Automated Machine which are manufactured by hydraulic pressure and with German Based dual vibration system which gives it high strength.
Technical Specification | |
---|---|
Thickness | 60mm, 80mm, 100mm |
Size Tolerance Limit | +/- 2 mm |
Water Absorption | Less than 7% |
Abrasion Resistance | Min. 1.5 |
Compressive Strength | |
60 MM | not less 35 N/mm2 |
80 MM | not less 40 N/mm2 |
100 MM | not less 50 N/mm2 |
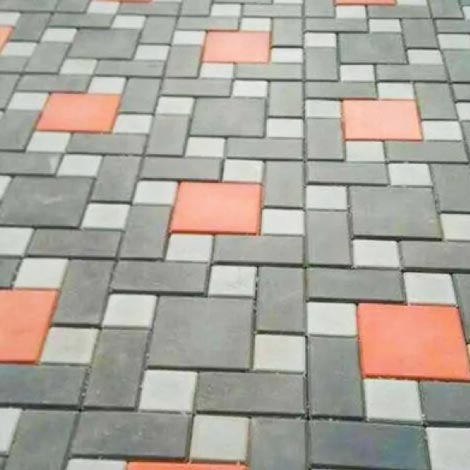
Advantages
- Highly Durable.
- Versatility.
- Easy to install.
- It comes in a variant Colour which makes it aesthetically pleasing.
- It is suitable for patchwork without disturbing the whole element.
- Power Paver Blocks naturally allows rain water to seep into ground.
- Not affected by thermal expansion or contraction.
- Maintenance is easy and simple and it is not affected by fuel and oil spillage.
- Use of coloured blocks facilitates permanent traffic marking.
Area of Applications
Non Traffic Area
Grade of Paver Blocks :- M25-M30 :
Footpaths, Malls, Public Garden / Parks, Bus Terminus, Railway Platform etc.
Medium Traffic
Grade of Paver Blocks :- M35-45 : City
Streets, Service Stations, Market Road, etc.
Heavy and Very Heavy Traffic
Grade of Paver Blocks :- M45-55: Heavy Loads on Road like Containers, Ports, Mining Areas, Factory Floors, Airport Pavement, Fuel Stations etc.
Types of Power Paver Blocks
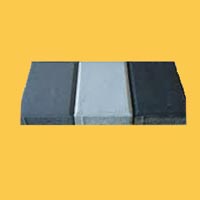
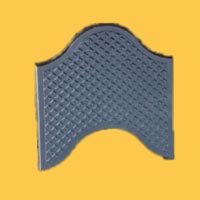
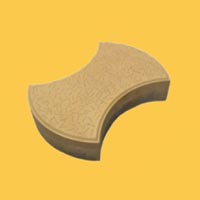
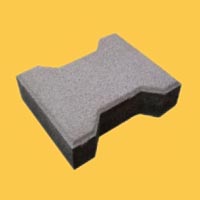
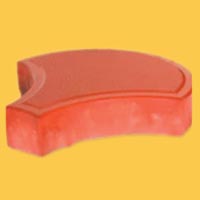
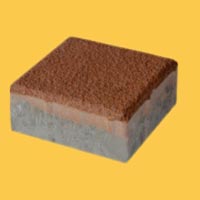
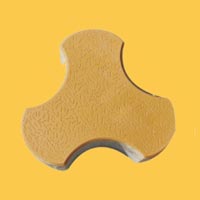
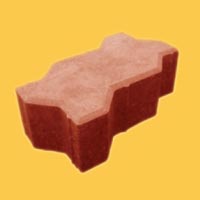
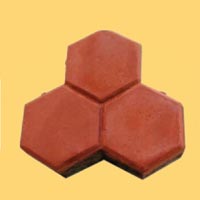
Shapes of Power Paver Blocks
- Trihex Grooves
- Rectangular Eta Shape
- Triangle Shape
- Square Shape
- Crown Shape
- Colorado Shape
- Europa Shape
- Marigold Shape
- I shape
- Zig Zag shape
- etc
- Trihex Grooves
- Rectangular Eta Shape
- Triangle Shape
- Square Shape
- Crown Shape
- Colorado Shape
- Europa Shape
- Marigold Shape
- I shape
- Zig Zag shape
- etc
Application of Power Paver Blocks
Preparation of the Substrate: The substrate or the concrete surface on which the paver blocks will be laid should be cleaned, levelled, and compacted to ensure a stable base for the blocks. A layer of sand or crushed stone may be added to provide a level surface and to improve drainage.
Installation of Edging: Edging should be installed around the perimeter of the area where the paver blocks will be laid to provide stability and to prevent the blocks from moving.
Mixing of Sand: A layer of sand should be spread over the substrate to a depth of about 50 mm or as per standards. The sand should be levelled and compacted to ensure a stable base for the paver blocks.
Laying of Paver Blocks: The paver blocks should be laid on the sand, starting from one corner and working towards the opposite corner. The blocks should be laid level and plumb, with consistent joint widths and depths.
Cutting of Paver Blocks: If necessary, paver blocks can be cut to fit specific dimensions using a masonary saw or other appropriate cutting tools.
Jointing of Paver Blocks: The joints between the paver blocks should be filled with sand or a suitable jointing material to prevent the blocks from moving and to provide a stable surface.
Compact the Paver Blocks: A vibrating plate compactor or similar tool can be used to compact the paver blocks and the jointing material to ensure a stable and durable surface.
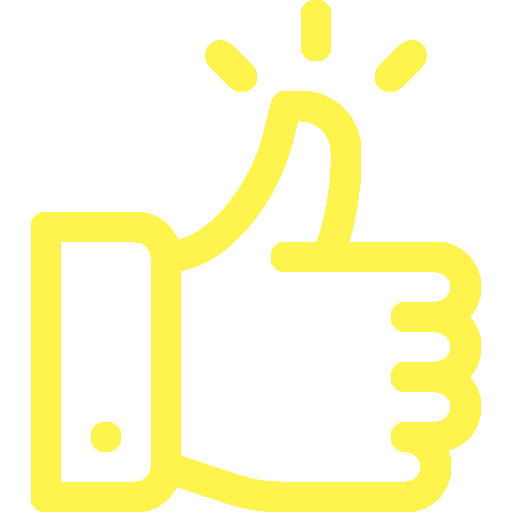
Do's
- 1. Do plan and design your project carefully, taking into account the intended use of the area, the size of the pavers, and any patterns or designs you want to create.
- 2. Do prepare the ground properly before installing the pavers, making sure it is level, well-drained, and free of debris.
- 3. Do use the correct type and amount of base material for the specific application, following the manufacturer’s recommendations.
- 4. Do use proper tools and equipment to cut and shape the paver blocks as needed.
- 5. Do seal the pavers after installation to help protect them from the elements and extend their lifespan.
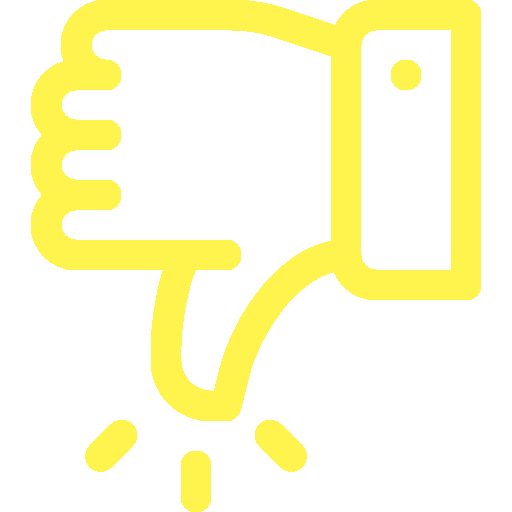
Don'ts
- 1. Don’t rush the installation process, as this can lead to mistakes and a subpar end result.
- 2. Don’t use the wrong type of base material or use too little of it, as this can cause the pavers to shift or sink over time.
- 3. Don’t use excessive force when compacting the base material or the paver blocks themselves, as this can damage the pavers.
- 4. Don’t use acid-based cleaners or harsh chemicals to clean the pavers, as this can damage the surface of the pavers.
- 5. Don’t exceed the recommended stacking height for the pavers, as this can make the installation unstable and unsafe.
Safety Measures
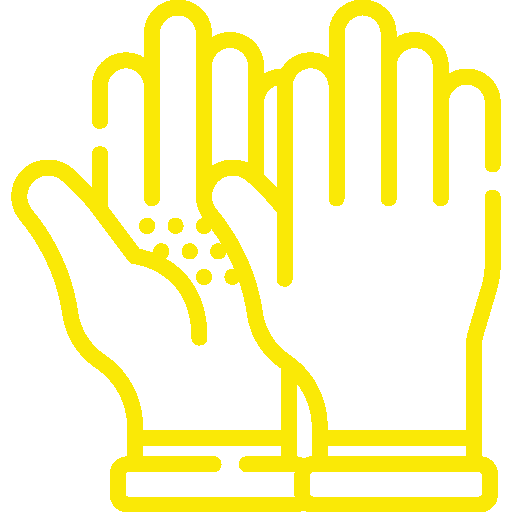

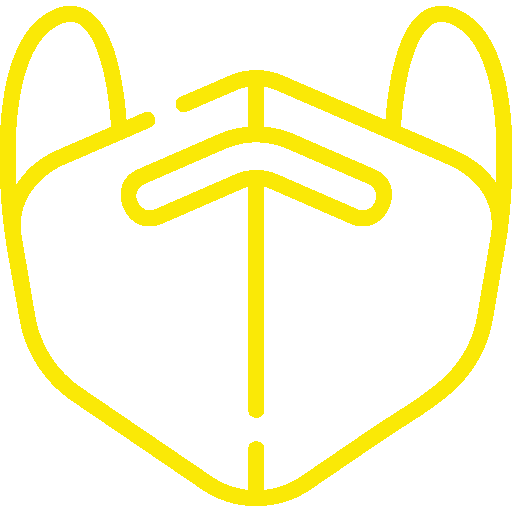
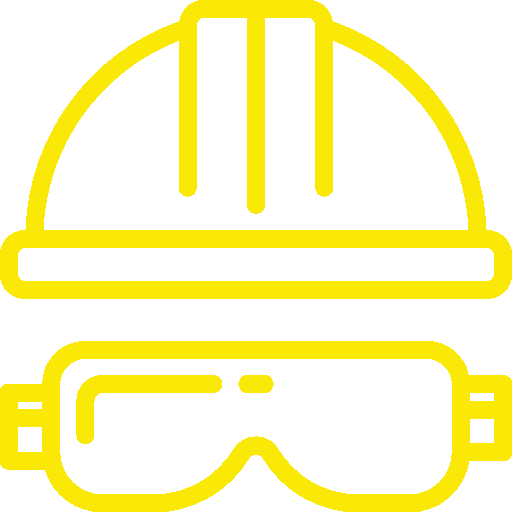
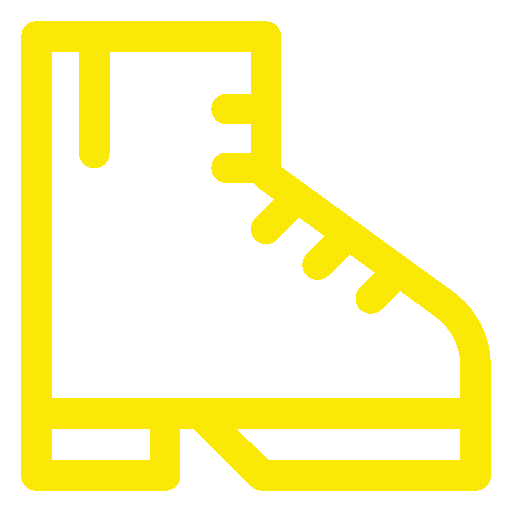
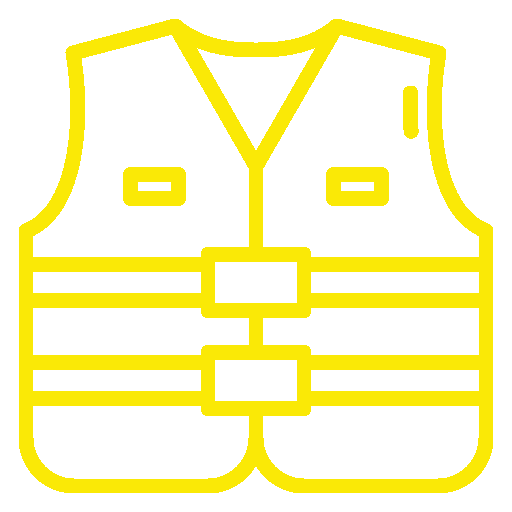
Safety Precautions While Fixing Power Paver Bricks
- 1. Wear Protective Gear: Always wear gloves, eye protection, safety Shoes and a dust mask when handling fly ash bricks and mortar, to protect against dust and other particles that can be harmful to your health.
- 2. Use Safe Lifting Techniques: When lifting blocks, use proper lifting techniques to avoid injury. Get help from a partner if necessary, and use a wheel barrow if available.
- 3. Be Careful with Tools: Be careful when using tools, such as hammers, chisels, and saws, to cut or shape the blocks. Use the proper technique, and ensure that the tools are in good condition before using them.
- 4. Avoid Electrical Hazards: Avoid electrical hazards by keeping electrical cords and tools away from the wet area.
- 5. Follow Safe Laying Techniques: Follow safe laying techniques when laying the bricks, including using a level, ensuring uniform joints, and cleaning the bricks after laying.